Maintenance is an Essential part of Business
According to the Cambridge dictionary, Maintenance means “work that you do to keep something in good condition”. Since the First Industrial Revolution (1760), when machines entered in people’s daily life, individuals have strived to maintain the machinery in the correct operating conditions and found that the way to keep it working for a long time was by performing maintenance work.
Nevertheless, many companies keep struggling to implement maintenance strategies because of the costs that this entails, the hard-to-change corporate cultures and the lack of training.
But failures can be expensive
The failure of a single component can cause the breakdown of other components resulting in the need for more complicated and prolonged repairs.
Analysing the chart, although capital savings may increase since no maintenance techniques or inspections are performed, the downtime resulting from the breakdowns is a huge cost driver. Another downside of waiting until the machinery fails is that restoring it to perfect operation conditions may be more expensive than maintaining its condition with systematic and planned actions.
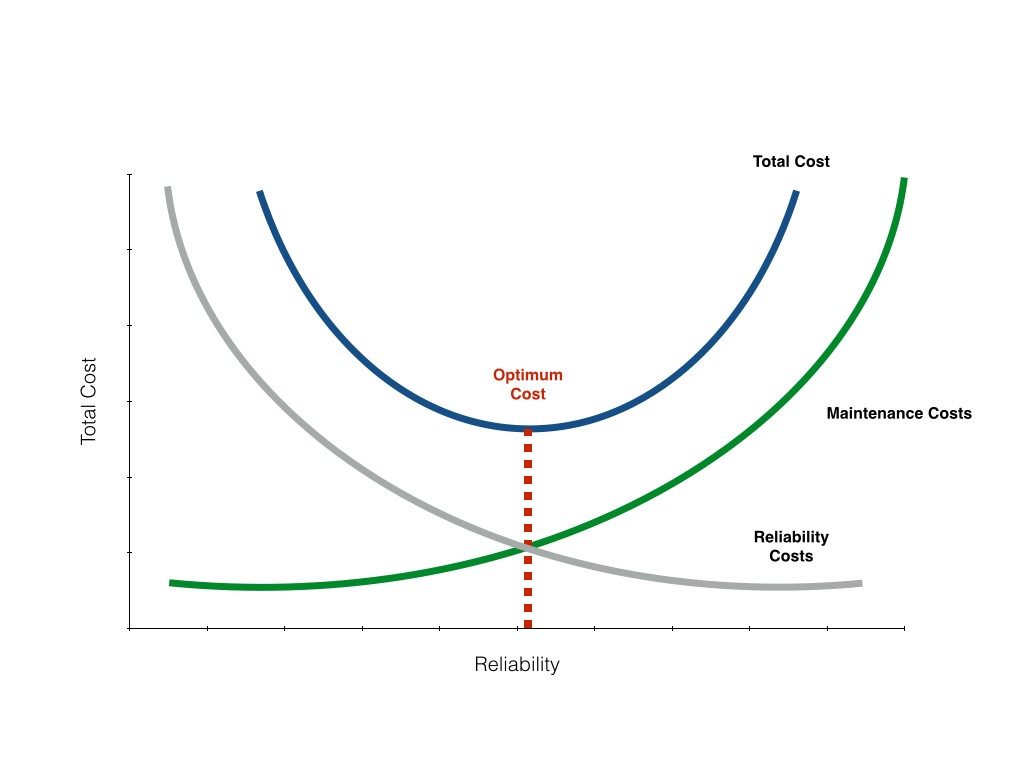
Companies have to look at maintenance as an investment rather than a cost, as in the long run, it can save money, time and stress caused by downtime. A new report from The Swedish Club shows that incorrect maintenance and repair continue to be the most frequent cause of main engines damage – a trend which has continued unabated since the Club began monitoring the issue nearly ten years ago.
The main goals of maintenance are:
- Reducing unplanned downtime;
- Extending machinery life;
- Minimizing Equipment damage/repair;
- Reducing Overtime;
- Reducing Repair Cost;
- Reducing parts inventory requirements;
- Improving reliability.
Prof. Al-Najjar from Lund University, Sweden, published a paper in 2007 where the role of maintenance in maintaining the quality of the essential elements in the manufacturing process is important, Prof. Al-Najjar concluded that condition monitoring is the form of vibration-based maintenance which can “enhance production and maintenance performance continuously and cost-effectively”.
Maintenance Concepts
Whether talking about the maintenance of a vessel main engine or a plant engine, there are different maintenance concepts that can be applied to both. Choosing the right strategy for a specific field, system or part can be intricate. The main goal is to keep the machinery at the optimum operating conditions with the least effort possible.
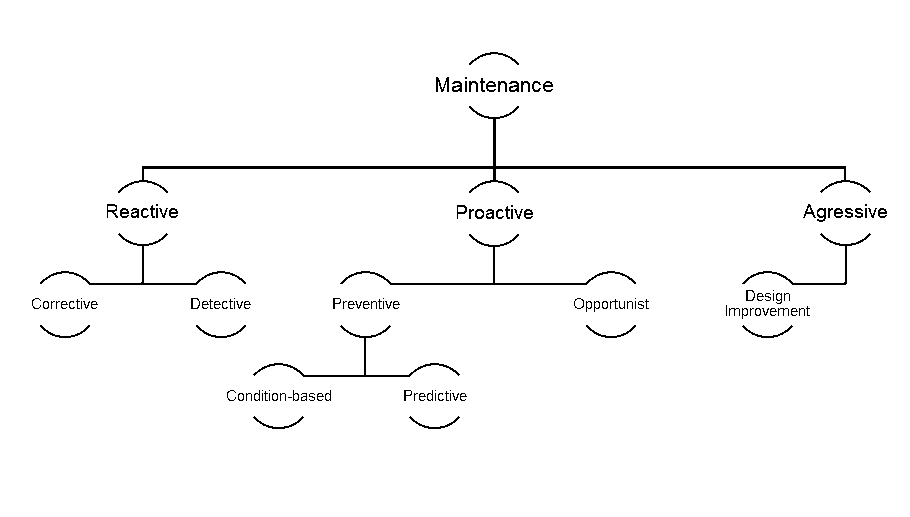
Despite the fact that all maintenance concepts have advantages and disadvantages, the important is to carefully analyze each one and identify which is more appropriate to each situation. All exist to reduce failures and the related costs but none can eliminate failures.
On this article, we will focus on the Preventive Maintenance and its derivatives, the Predictive and the Condition-based Maintenance.
Preventive
The Preventive Maintenance prevents failures from occurring by applying maintenance beforehand and thus avoiding a system breakdown causing downtime. This can be done in a predetermined and a predictive way.
Predictive
The goal of predictive or condition-based maintenance is to observe the system’s condition in order to plan the necessary maintenance. To establish the right representation of the current condition, condition monitoring has to be applied.
Like any other concepts, predictive maintenance has advantages and disadvantages and is not suitable for all sorts of systems. One of the benefits of predictive maintenance is that it can prevent failures. By detecting a developing failure or fault a breakdown can be prevented.
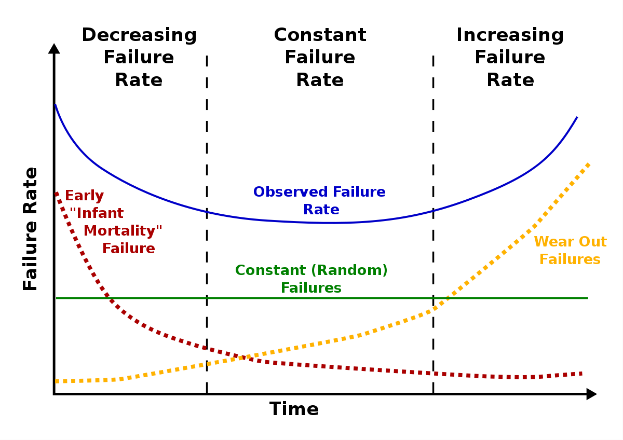
Condition Monitoring
Condition monitoring, as the base of predictive maintenance, extracts information concerning the health of the system from the measured condition, and based on this information, the need for maintenance in the future can be predicted.
Its purpose is to detect and follow-up developing faults and anticipate upcoming failures and possible breakdowns. In that way, maintenance can be planned in time to prevent extra costs and optimize the operation. The most commonly used techniques in Condition Monitoring include vibration monitoring, process parameter monitoring, visual inspection, tribology, and thermography.
Diesel Engine Condition Monitoring
The Condition Monitoring methods can be applied to several types of machinery. For diesel engines specifically, some methods are more suitable than others and for every component, another monitoring method can be more applicable.
That is why the division into different methods is made according to the different components to be monitored, such as:
- Fuel injection process;
- Cylinder combustion process;
- Lubrication system;
- Mechanical components;
- Heat exchanger;
- Air and gas path processes.
- Every component has its own parameters, faults, and failure consequences.
Fuel Injection Process
This process is crucial for the operation of the engine because if the injection timing is incorrect or the valves are leaking, problems such as thermal overload may occur. A problem while performing condition monitoring of the fuel injection equipment is the fact that it is very small spaced and placing sensors can be difficult. Also, pressure, temperature, and frequency are high which makes it difficult to find a sensor that can survive this harsh environment for a long period of time.
Cylinder Combustion Process
The combustion is the engine driving process and, therefore, the heart of the diesel engine. If a failure occurs inside the cylinder, a complete breakdown is inevitable. A lot of information can be measured by the combustion process such as the temperature and pressure in relation to time, angle, and volume. Also, the output of the engine tells a lot about what is happening in the cylinder. Although monitoring is the best option, the environment in the cylinder is the roughest in all the engine, which requires a good monitoring strategy.
Lubrication System
The lubricant system is the vein system of the engine. Most of the moving components inside the engine and the surrounding parts need to be lubricated. The quality of the lubrication oil influences the wear on the parts and therefore can lead to an indirect failure.
Mechanical Components
The mechanical system of a diesel engine mainly concerns the bearings and piston rings. The bearings are experiencing high loads and they are continuously exposed to wear. This can lead to cracks and, eventually, failure of the component. A bearing failure in a marine diesel plant can force the vessel to stop.
Heat Exchanger
Monitoring the heat exchanger is performed more in terms of performance than condition monitoring. If the heat exchanger faces a fault, this will affect the performance of the engine and might even lead to failure.
Air and Gas Path Processes
Monitoring the air and gas path processes inside the engine can reveal possible faults but also optimize the performance. Reduced air flow can cause problems like thermal overload, leading to degradation of the materials. However, placing sensors in the flow path is very difficult because of the high pressures and the temperatures making it a harsh environment for sensors. By measuring the composition of the exhaust gases, a range of malfunctions can be uncovered like timing and fuel quality.
Diesel Engine Monitoring Systems
Over the years many different diesel engine condition monitoring systems have been developed.
Most of the diesel engine condition monitoring systems have been established for the marine industry. The reason is that high reliability is demanded on board to prevent loss of propulsion and maintenance should be carefully planned to match the sailing program. These systems are also implemented in the industry to diminish failures during the process of manufacturing.
BOEM-S, among several other features, is a condition monitoring system developed by TecnoVeritas that can be applied to both sectors because of its flexibility and highly customizable features, responding to each client needs. Also EDS system – a portable Engine Diagnosis equipment – allows to monitor and diagnose engines in real time and assure our clients of their engines condition.
The BOEM-S
BOEM-S is an online platform that allows companies to continuously monitor their assets, from environmental conditions to engine parameters such as Brake Mean Effective Pressure (BMEP), Rotating Speed, Oil Temperature and many more. On top of that, with BOEM-S, business managers and leads can schedule and document maintenance operations allowing a much more practical and simple approach to asset management. In addition, the state of that asset can be effectively monitored, giving the owner the capacity to evaluate its performance.
BOEM-S uses the readings of installed machinery key sensors for the evaluation of the machinery condition, and the data collected is used to monitor machinery condition, generating condition alarms. Examples of this may be the assessment of main engines turbocharger efficiency, condenser and boilers or turbocharger vibrations, among other equipment’s.
The system uses artificial intelligence, learning as it gathers operational information about each ship/plant machinery, making the prediction accurate and reliable. The crew/team can manage the ship/plant maintenance, including tasks scheduled, technical instructions, required manpower, tools, time, spare parts, budgets, and reports. One of the features of BOEM-S is that the system is cloud-based, meaning it is accessible everywhere with any device.